An awareness of the impact of materials selection on the machining processes for small, complex components can affect overall end-product quality and costs
The importance of material selection for small, complex components found in equipment critical to the chemical process industries (CPI) cannot be understated. For small metal parts, such as valves and threaded fasteners, the steps product engineers take for selecting a material are fairly linear. The engineer determines the functionality and the operating environment of the components and chooses the material. Environmental factors taken into consideration include corrosion resistance, exposure to harsh chemicals and extreme temperatures. After evaluating the material based on these conditions, design engineers often make the final material decision for the specific part. However, the desired material may have certain properties that can present challenges in operation and machining, and the designer may not be aware of the potential issues that can arise.
There is an important relationship between material selection and precision, ease of machining and final finish that is often overlooked. These factors can have significant effects on the quality and cost of the component in question. The use of an ineffective machining method for small components can cause issues in certain materials, especially if they are exotic or hard-to-machine metals. These issues include fouled operating environments, premature component failure and oxidation effects, and are sometimes the result of inadequate machining and material selection. This article provides guidance to help design engineers consider the relationship between material selection, existing machining processes and the quality and cost of the end product.
MATERIAL SELECTION FACTORS
Functionality in the operating environment is generally a high priority for material selection of components, especially when it comes to the long- and short-term safety and reliability of the equipment. The following sections introduce some important factors that must be considered in material selection for small, complex components.
Corrosion resistance. Corrosion is a major concern that dictates material selection in many operating environments. For example, chloride ions cause stress corrosion cracking (SCC) in stainless steels, so a material like titanium is selected because of its chloride-resistant properties. These factors are critical because corrosion in equipment can result in a number of negative effects, including fires, explosions and both brittle and mechanical failures, as well as the release of hazardous gases, liquids or vapors.
Oxidation is commonly observed in materials like the stainless-steel alloys. These metals naturally form oxide layers for corrosion protection, which can cause uneven surfaces. This occurrence requires passivation treatment to reduce the negative effects of these oxide layers and to keep the surfaces smooth and free of imperfections that can cause equipment failure.
Exposure to chemicals.Materials can have adverse reactions to chemicals in various environments. Environmental chemical factors can include high acidity and the presence of oxygen or aqueous solutions, or even harsh cleaning or sanitizing agents. Although the production environment may be non-corrosive, the presence of these chemicals can cause materials to react, so a designer should consider the risks when selecting materials.
Temperature resistance. The engineer should be aware that the mechanical limits of materials can be negatively affected by high temperatures, potentially causing thermal failure or deformation. Materials are also selected based on temperature resistance because the effect of extreme temperatures on materials can cause increased corrosion rates. High-temperature materials include iron-, nickel- and cobalt-based metal alloys.
Cost. A major factor in the materials-selection decision typically involves the initial cost of the material, the ease of machining and repair and the availability of the material. Cost influences the balance between materials and machining in the case of material grades. For example, if an engineer chooses Inconel as the material for the product, the grade affects the machining cost. Since Inconel 600 is much easier to machine than Inconel 718, the time and cost of machining can change considerably depending on which grade is chosen. Figure 1 shows some threaded parts that are constructed of Inconel 718. However, note that cost is usually secondary to the other considerations that involve consistent and reliable operation of the part in its application.
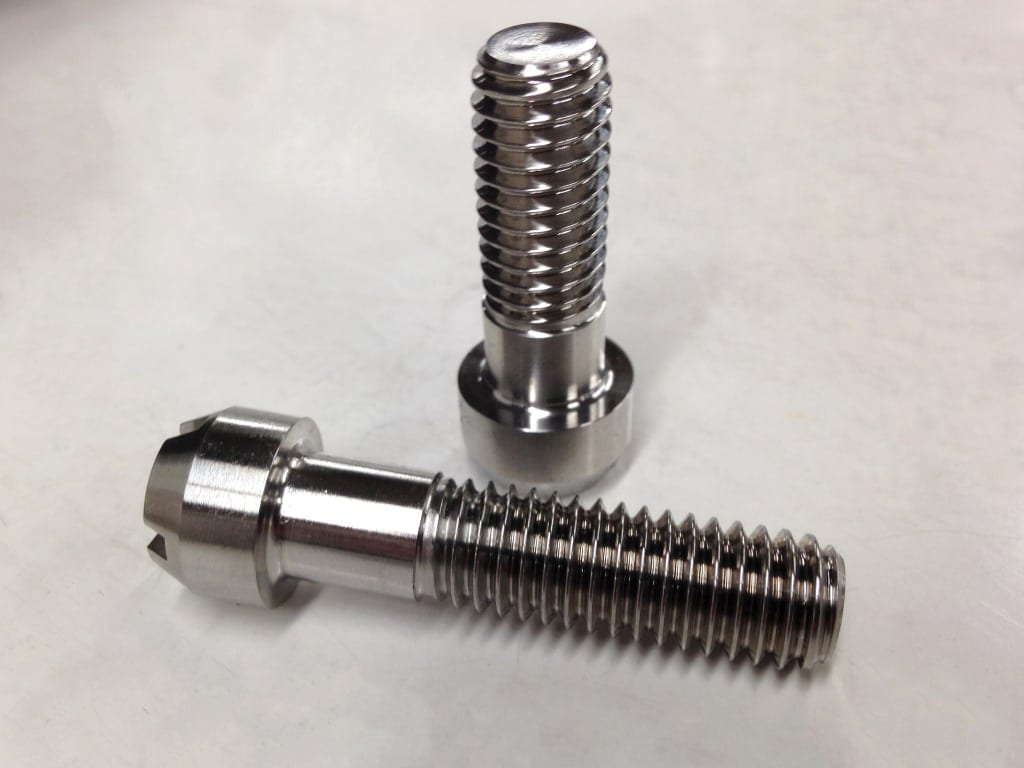
Restrictive applications.In most CPI applications, the selection of the appropriate material can usually prevent the negative effects associated with the operating environment, but some applications are more restrictive. Due to strict operating-environment protocols, designing parts for certain applications, such as nuclear processing, can be limiting when it comes to choosing a material. Areas at risk for fire or explosions, such as oil-and-gas processing facilities, are also restrictive when considering equipment material. Certification systems, such as the International Electrotechnical Commission’s (IEC; Geneva, Switzerland; www.iec.ch) globally recognized System for Certification to Standards Relating to Equipment for Use in Explosive Atmospheres (IECEx System; www.iecex.com), may require the provision of specific material properties to improve equipment and personnel safety.
The most common class of materials chosen for chemical processing equipment is metal, because metal materials are typically stronger, more resistant to fatigue and cracking, and are typically easier to machine than other material classes, such as glasses, polymers and ceramics.
For small threaded parts (such as threaded valve connectors) that play a significant role in the performance and longevity of chemical processing equipment, metals are most often selected for these properties. However, in some precision equipment, such as gears, ceramics and other hard materials are corrosion-resistant and can achieve equal or better surface finishes than some metals. Other non-metallic materials, such as high-performance polymers, are used in place of metals to reduce the weight of equipment.
THREADED PARTS AND VALVES
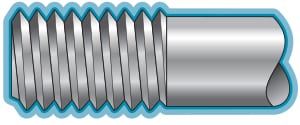
FIGURE 2. Threaded parts must be able to withstand a number of harsh conditions in CPI applications, including exposure to corrosive materials, high temperatures and pressures and other environmental restrictions
Threaded parts (Figure 2) and valves are used in processing equipment in countless CPI applications, but can often be overlooked. An understanding of these complex parts gives engineers insight into the materials-selection and machining processes.
Fasteners and threads. Fasteners and threaded parts can be the smallest parts in chemical processing equipment, but are often critical to the assembly of larger equipment. These components must be strong, durable and corrosion-resistant to ensure that equipment performs safely and reliably. As mentioned, exotic metals, including stainless-steel alloys, titanium and Inconel, which have greater resistance to harsh chemicals and can endure very high temperatures, are examples of desirable materials for fasteners used in heat exchangers, exhaust systems, tanks, vessels and other processing equipment. Mechanical properties, such as high strength-to-weight ratios, will also lead a designer to choose an exotic metal.
Valves.Valves are highly involved in chemical processing equipment, such as the piping systems that control the flow of liquids, gases and vapors. Valve systems can be very complex, with multiple parts and components, and each one must perform as expected by resisting corrosion and fatigue. In harsh chemical-processing applications, valve systems are often custom designed to maintain pressure levels and prevent dangerous, and sometimes lethal, fugitive emissions. The control of fugitive emissions, no matter how small, is a major concern for plant engineers because they can be harmful to personnel, equipment and the environment.
Many of the basic external and internal components of a valve system depend on strong and tight threaded joints and connections for safe, reliable and efficient performance under demanding operating environments. An example of a threaded component in a valve is the valve body. Valve bodies make up the structural foundation and contain the internal components of most pressure valves. They are connected to piping via threaded or welded joints. The body is commonly attached to the valve bonnet with threaded connections. The bonnet houses the valve stem. Valve stems are typically attached to a disk (or ball, depending on the valve type) via threads. As the threaded stem spins into or out of the valve bonnet, the disk moves, controlling the chemical flow. The seal between the stem and disk must be tight, and uniform thread finishes are important to prevent leaks.
To ensure peak performance of these complex components, exotic metals are chosen. However, the selection of these exotic metals can present additional design challenges related to machining that design engineers are often unaware of that can negatively impact product quality and inadvertently drive up costs. Figure 3 depicts internal components from a high-pressure gas valve that are constructed of 316 stainless steel.
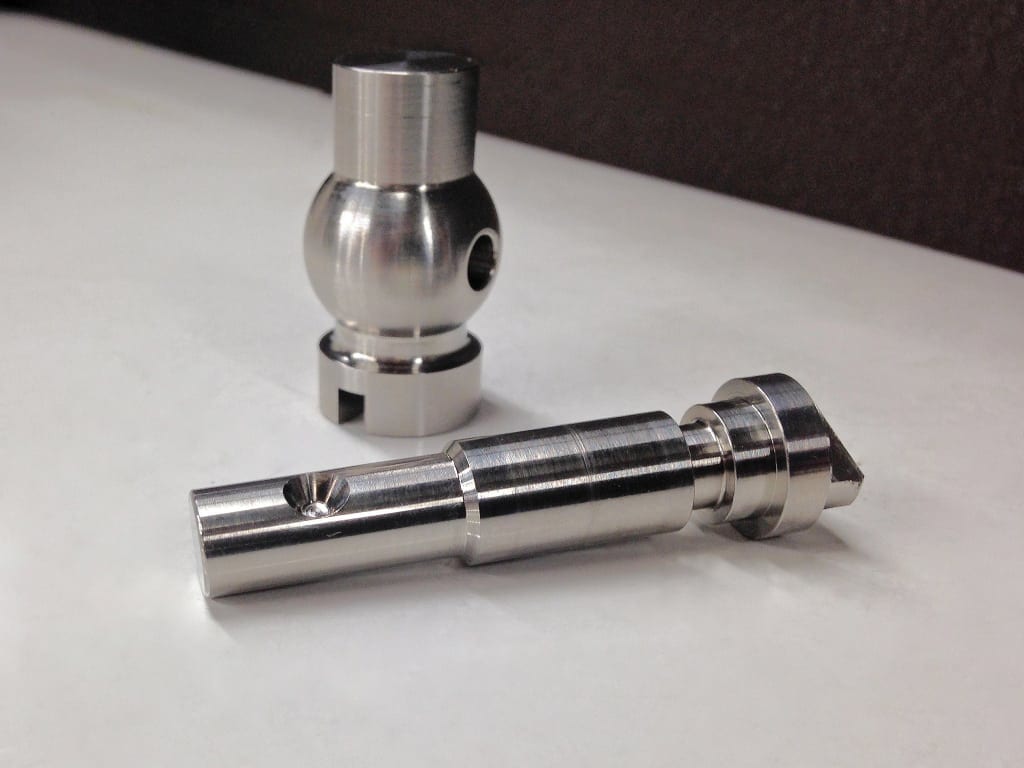
FIGURE 3. Stainless steel provides many beneficial properties for valve internals, but this material can pose challenges for machining processes
MACHINING SPECIFICATION
For threaded parts, it is common for design engineers to leave the machining method unspecified on a request for quote (RFQ) or design specification. The method is then left up to the machine shop to decide, which can result in missed opportunities for the designer to avoid premature failure, improve product quality and reduce costs, especially if the selected materials are difficult to machine. Knowing the available machining options can help a designer to make the most appropriate design choices.
Machining method options. The two most common methods for the machining of external and internal threads are cutting and rolling. Thread cutting is a process in which a sharpened cutting tool is used to physically remove material from a blank, metal round bar or hole to form threads. This results in the production of rough, uneven threads with microscopic chips that can flake off and foul the operating environment or cause excessive friction.
Thread rolling is a work-hardening process in which flat or cylindrical dies apply great amounts of pressure to the blank material, forcing the material outward into the shape of threads. Because the material is displaced instead of removed, rolled threads are typically hardened and have smooth finishes. Figure 4 illustrates the physical differences between parts that undergo thread cutting and thread rolling.
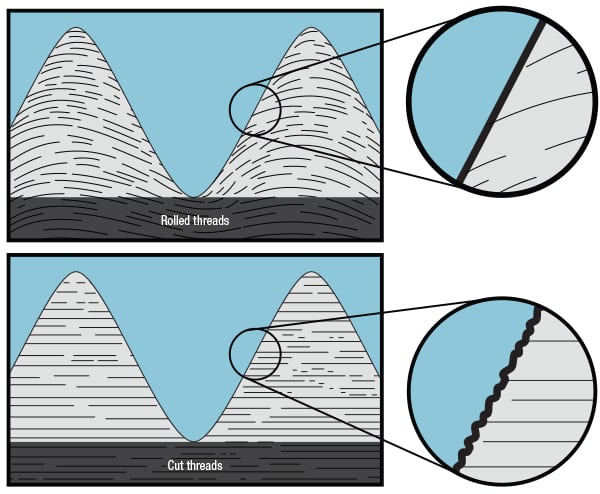
In CPI applications that require thread accuracy, rolling has significant advantages over thread cutting. Rolled threads have smooth finishes, very tight tolerances, superior strength, resistance to fatigue and consistent thread geometry — all desirable properties of equipment used for chemical processing. Thread accuracy and consistency is critical for any harsh environment. When assembling a product, ensuring consistent flow and preventing leakage results in a more reliable and efficient final product. This will not only improve the safety of personnel, but it will also reduce the loss of expensive chemicals. Consistent surface finishes also prevent harsh chemicals from attaching to imperfections, pits or tool marks on the metal surface.
At this point, a design engineer may ask: how does thread rolling relate to material selection? As mentioned, metals are the most commonly chosen material class for the design of chemical processing equipment. Despite being more corrosion-resistant, stronger and resistant to fracture, metals can also possess qualities that make them difficult to machine. Because the CPI count on many types of metals for safety and reliability, choosing the most suitable machining method for specific materials is important for the design of threaded parts and valves.
MACHINING SOLUTIONS
As previously discussed, exotic and hard-to-machine metals, such as stainless steels, titanium and nickel-based alloys like Inconel, are often chosen due to their physical properties’ capabilities in the required application. However, these materials also have various undesirable properties that can create challenges.These potential issues can usually be overcome by selecting the correct machining method.
Ease of machining.Ductility, or a material’s ability to deform without fracture, is a major property that determines its machinability. Steels and nonferrous metals that are less ductile will typically break and produce chips and impurities as material is removed. As a result, thread cutting is a very ineffective method of machining for these materials. Although these metals do not deform easily and require much greater amounts of pressure to form threads, they typically roll very efficiently and yield the consistent thread geometry and smooth surfaces that are desirable for equipment components used in the CPI. The ductility of a specific material can be acquired from an ASTM International test.
Smooth surfaces. When a material is cut, the microscopic particles that are left behind can cause thread galling. Galling is a form of wear caused by the sliding and friction between two metal surfaces. Unlike some forms of wear that occur over time, the negative effects of galling will be observed as soon as the metal parts are assembled and in sliding contact. When a metal surface galls, microscopic particles break off and foul the operating environment. Galling is most common in ductile metals like aluminum compounds, because particles are more prone to transfer during motion.
Although these ductile metals are more likely to gall, the high pressures of the dies during the thread-rolling process makes the metal surfaces harder and denser. This means that the presence of microscopic particles that typically form during the machining of ductile metals is significantly reduced. Choosing thread rolling is a strategy that a designer can take prior to production that can result in smooth surfaces on various types of metal fasteners and threads.
Protecting against oxidation. As discussed, oxide layers form in many types of metals, such as stainless steel, titanium or aluminum, for increased corrosion protection. However, this can cause significant issues for threads and mated parts.
If the surfaces of the threads have impurities or imperfections, they will cause increased friction as parts tighten. This causes the oxide films on the surface to be scraped away, leaving behind damage to the underlying layers of metal. These damaged and exposed layers are prime starting points for galling. Typically, surface finishes are used as a preventive measure, but in many chemical-processing applications, such as food or pharmaceutical processing, the selected finish must meet the regulations of the U.S. Department of Agriculture (USDA; Washington, D.C; www.usda.gov) or the U.S. Food and Drug Administration (FDA; Silver Spring, Md.; www.fda.gov) to avoid contamination. In these cases, thread rolling can be a means of eliminating the impurities that can adhere to these surfaces and cause oxide layers to come apart.
Complete material isolation. In CPI applications, the isolation of material is often critical, so valves are used to constrain the flow of gases, liquids or vapors to a specific location. These isolation valves require highly reliable shutoff and sealing capabilities in order to prevent dangerous leaks in harsh operating environments. Application-specific materials may prevent corrosion, but rolled threads can help to ensure stronger seals and connections.
Rolled threads are work-hardened without the removal of material, so the natural material grains are left unbroken and continuous. As a result, these threads have much higher yield strengths and tighter tolerances than that of cut threads. The uniform thread geometry of rolled threads allows parts to fit together better, with fewer chances for sliding or loosening. Depending on the ductility of the material, tolerances of rolled threads can be as tight as±0.015 mm. These tight tolerances are ideal for threaded valve joints and connections that require reliable material isolation and shut-off.
Production costs.As with material selection, the selection of the machining method can impact costs. The thread-rolling process is much more efficient than cutting, and in some cases can result in 90% decreases in production times. Unlike the cutting tools that must be sharpened and reset periodically during machining, the dies used for rolling can continue production for long periods of time. Die lifetime is an important factor in considering machining costs. Figure 5 shows an example of some internal components from a high-pressure fog valve that are constructed of 316 stainless steel. For such components, the designer has the option to specify full thread crest, if required. However, if an application does not require full thread crest, the costs will be lowered because the die life is increased when the crest is not full. This has no impact on the effective portion of the thread. Full thread crest was not specified for the components in Figure 5.
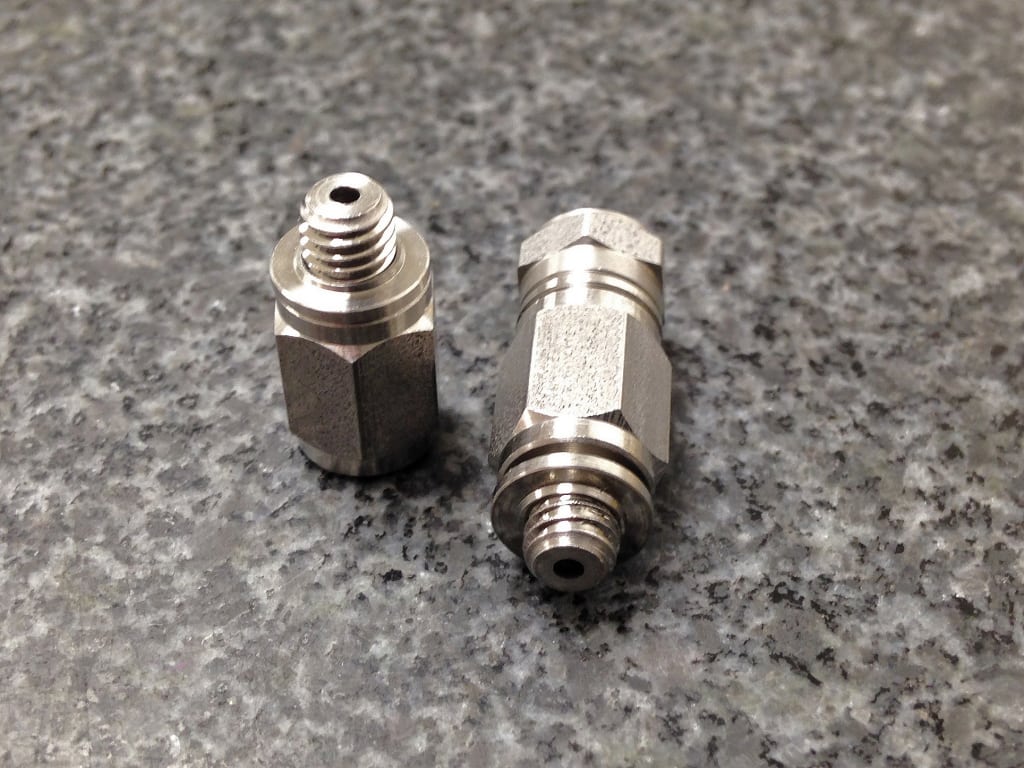
The accuracy of rolled threads is another factor that makes them cost-effective, because the need to frequently inspect threads for consistency during production runs is eliminated. This saves on costs of labor. By rolling threads, the design engineer will observe the exact same thread geometry for the first part as the last.
An understanding of the intended functionality and operating environment is significant in deciding on a material for a small threaded part or valve component in the CPI, but this is only part of the process. Going a step further in the design of these components by specifying the machining method is another way of ensuring that the part will operate at peak performance when manufactured from the desired material.
No comments:
Post a Comment